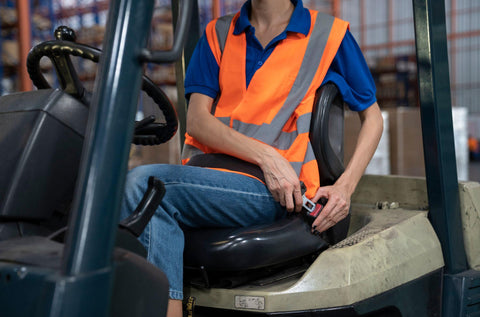
When it comes to operating forklifts, safety is paramount. Despite their robust appearance and essential role in material handling, forklifts pose significant risks to operators and bystanders alike, including the potential for serious injuries or even fatalities.
A common point of discussion and sometimes confusion is the use of seat belts on forklifts. Why, in the relatively confined spaces of warehouses and construction sites, where speeds are inherently lower than on open roads, are seat belts deemed necessary?
Below, we’ll delve into the critical reasons behind the inclusion of seat belts in forklift safety protocols, addressing the regulations that mandate their use and the safety benefits they provide.
The Importance of Forklift Safety
Forklifts are indispensable in various industrial, construction, and warehousing settings, efficiently moving heavy materials over short distances. However, their operation is not without risks. Forklifts can easily tip over if improperly loaded or maneuvered, posing a significant risk not only to the operator but also to nearby workers.
Furthermore, the busy environments in which forklifts operate can lead to collisions with pedestrians, other vehicles, or obstacles, each scenario carrying the potential for serious injuries.
The statistics are sobering; forklift-related incidents account for a substantial number of workplace injuries and fatalities annually. For example, it is not uncommon to hear about cases where a lack of proper safety measures, including seat belt usage, contributed to severe injuries or worse during forklift tip-over incidents.
These risks underscore the critical need for stringent safety practices, including the use of seat belts, to protect operators from being thrown from the vehicle or crushed under it in the event of a tip-over.
Unpacking the Legal Requirements
The Occupational Safety & Health Administration (OSHA) does not explicitly mandate seat belts on forklifts through specific rules but requires employers under the Occupational Safety and Health Act to protect employees from “serious and recognized hazards,” which includes the risk of being crushed—or “mousetrapped” in forklift overturns.
All powered industrial trucks manufactured after 1992 must have seat belts or similar restraint systems to mitigate this risk. This indirect requirement ensures employers equip forklifts with seat belts to comply with OSHA’s broader mandate to safeguard workers against recognized dangers, emphasizing the agency’s focus on preventing severe injuries or fatalities associated with forklift operations.
Why Do Forklifts Have Seat Belts?
Seat belts on forklifts serve multiple critical safety functions beyond the simple restraint of the operator. These safety features are integral to preventing accidents and reducing the severity of injuries when mishaps occur. Here’s why seat belts are essential in forklift operations:
- Prevention of Ejection: They keep operators securely within the forklift cabin during a tip-over, significantly reducing the likelihood of being thrown out and injured.
- Mitigation of Mousetrapping: Seat belts minimize the risk of operators being crushed between the forklift and the ground or another object in the event of an overturn.
- Enhanced Operator Safety: They contribute to overall safety by encouraging safer driving practices and minimizing the chance of risky maneuvers.
- Compliance with Safety Standards: Using seat belts ensures adherence to OSHA’s guidelines to protect workers from recognized hazards, helping avoid legal penalties and fostering a safety-first workplace culture.
- Promotion of Safe Operation: The presence of seat belts acts as a constant reminder of the risks associated with forklift operations, promoting a culture of caution and diligence.
Comprehensive Safety Practices in Forklift Operations
Beyond the use of seat belts, a comprehensive approach to safety within forklift operations incorporates various practices and protocols. These practices are designed to minimize risks and enhance the safety of operators and bystanders alike:
- Regular Maintenance Checks Ensuring forklifts are in optimal working condition, reducing the chance of mechanical failures that could lead to accidents, is essential.
- Proper Loading Techniques Operators need training on how to load and balance materials correctly, which is crucial for preventing tip-over incidents.
- Comprehensive Operator Training Extensive training on safe driving practices, recognizing potential hazards, and emergency response procedures are key to safety.
- Use of Warning Signals Implementing both visual and auditory warning systems alerts both workers and operators to potential dangers in the operation area.
- Pedestrian Awareness Programs Educating all personnel on maintaining a safe distance from operating forklifts and identifying safe walkways and zones promotes mutual safety.
Enhance Forklift Safety with Our Seat Selection
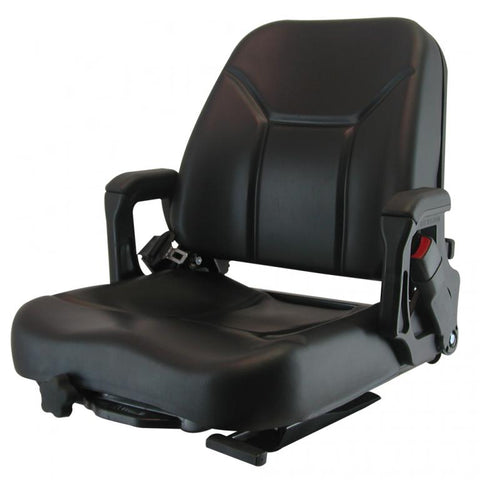
Seat belts play a pivotal role in forklift safety, crucial for preventing ejections, mitigating crushing hazards, ensuring regulatory compliance, and fostering a safety-first culture. Recognizing this, our company offers a premier selection of forklift seats with seat belts, including Toyota forklift seats, designed to meet the highest standards of safety and comfort.
By upgrading to our superior seats, businesses can significantly enhance operator safety and demonstrate a steadfast commitment to workplace safety. We invite you to explore our range and make a pivotal investment in your team’s well-being and your operation’s safety compliance.